
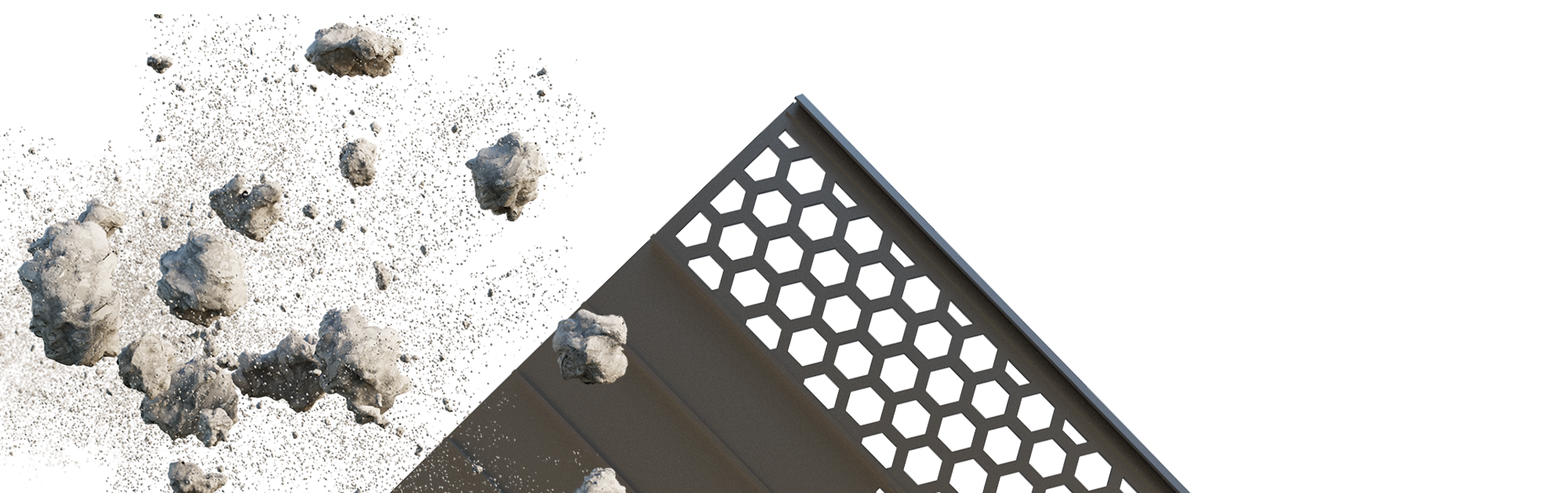

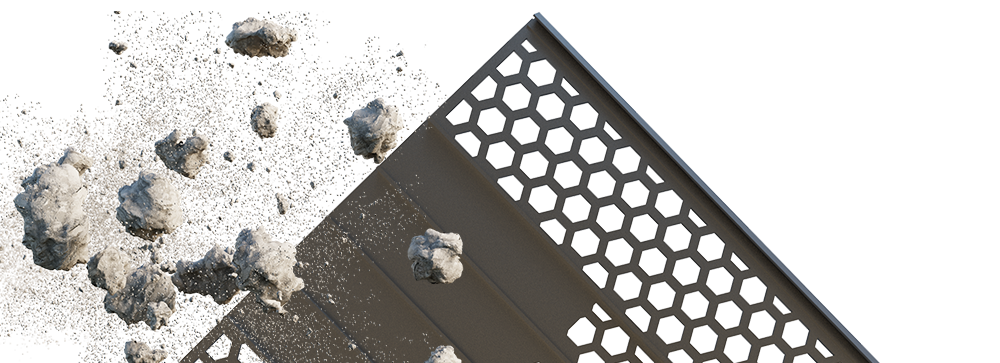

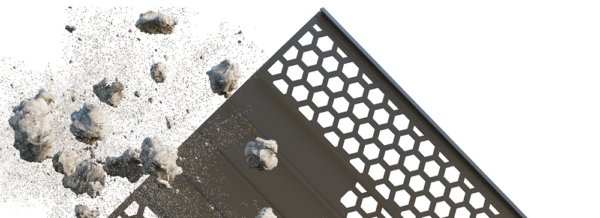
MAX-Out Wear Life
MAX-Out
Wear Life
There are certain screening applications that require nothing less than America’s Toughest Steel! With precision plasma burnt holes, in any shape or pattern, our through-hardened MAXWEAR Steel Perforated Plate screens (also referred to as Punch Plate) are designed to handle the highest impact and abrasion materials with ease – wearing 6-10X longer than woven wire!
MAX-Out Open Area
MAX-Out
Open Area
Did you know that a MAXWEAR Perf Plate screen can provide 6-10X longer wear life than a woven wire screen without compromising open area and that it can be installed anywhere that a woven wire screen can be installed, either flat or crowned? In fact, a correctly configured Perf Plate screen can actually increase open area over traditional woven wire!
When using woven wire, there will always be a tradeoff between wear life and open area – an increase in wire diameter will improve wear life but it will also reduce open area because the wire necessarily takes up more space. The thickness of a woven wire screen and the space between the holes will always be the same because they are both determined by the wire diameter. A MAXWEAR Perf Plate screen solves this problem because the thickness of the steel plate and the bar size are independent variables! It is possible to have closely arrayed holes in a thicker plate resulting in a longer wearing screen with more open area.
A MAXWEAR Perf Plate screen can also be repaired in the field, when necessary, further increasing the long-term wear life value of this rugged, versatile screen.
Eliminate Pegging & Blinding!
Eliminate Pegging
& Blinding!
Our state of the art, high definition plasma tables can create openings in any shape or pattern to solve just about any material challenge. Round, Hex, and Octagonal Holes virtually eliminate the pegging and blinding that the square openings in woven wire screens are so prone to. Additionally, we plasma burn each hole to be slightly conical in shape, meaning that the bottom of the hole is slightly wider than the top, further reducing the likelihood of material pegging.
Get it Fast!
Get it Fast!
Samscreen’s standard lead time on MAXWEAR Perf Plate screens is just 4 days! From the development of custom CAD drawings, to the moment that your screen goes out the door – our process is streamlined, accurate, and fast! Faster than anyone else in the industry!
MAXWEAR™
For your toughest jobs
Perforated Plate
WHEN YOUR PROBLEM IS…
Woven Wire Wearing out too quickly + Pegging
YOUR SOLUTION IS…
America’s toughest steel plate, with HD Plasma Burnt perforations in exactly the shape, size, and pattern you need for your unique job
Installations
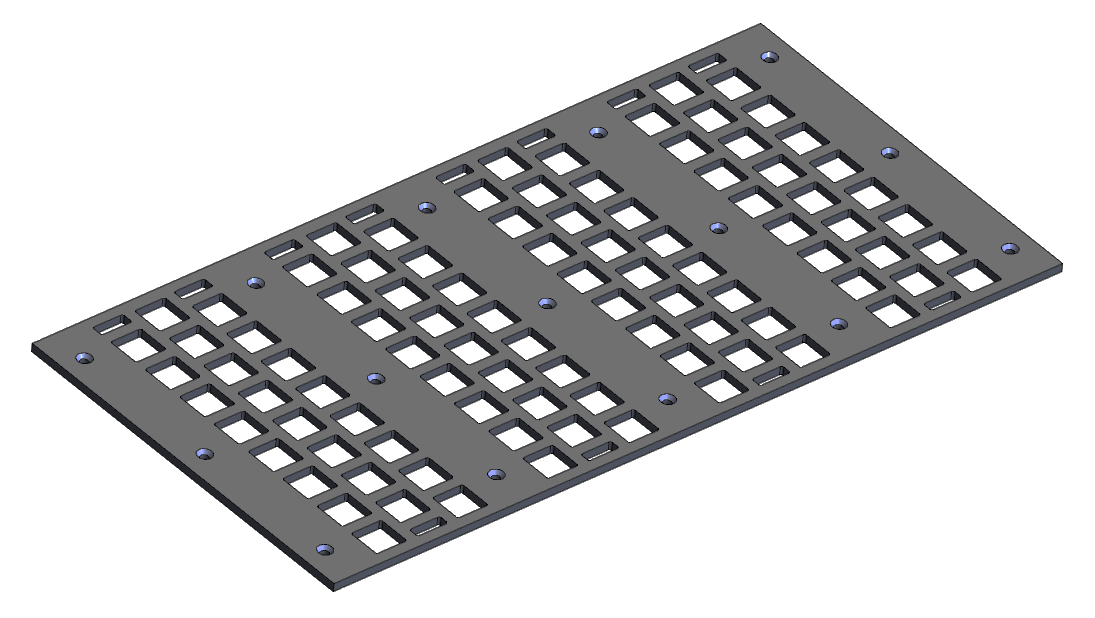
Bolt-Down
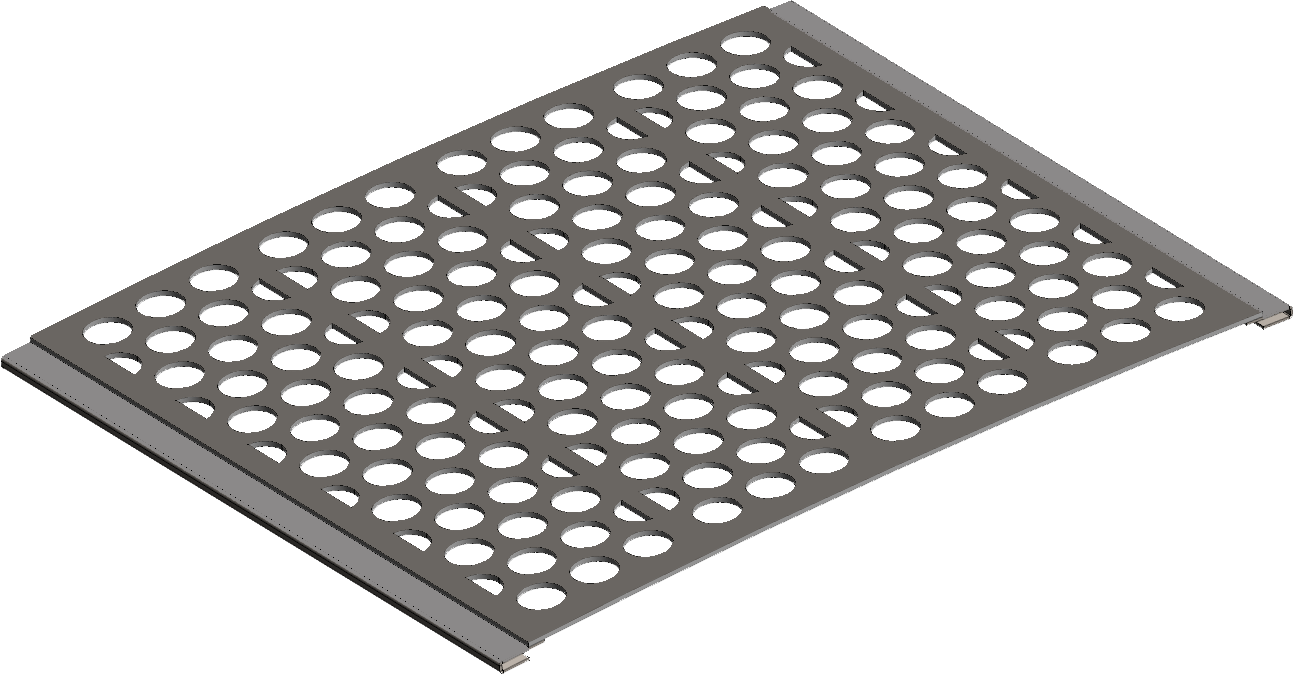
End-Tension
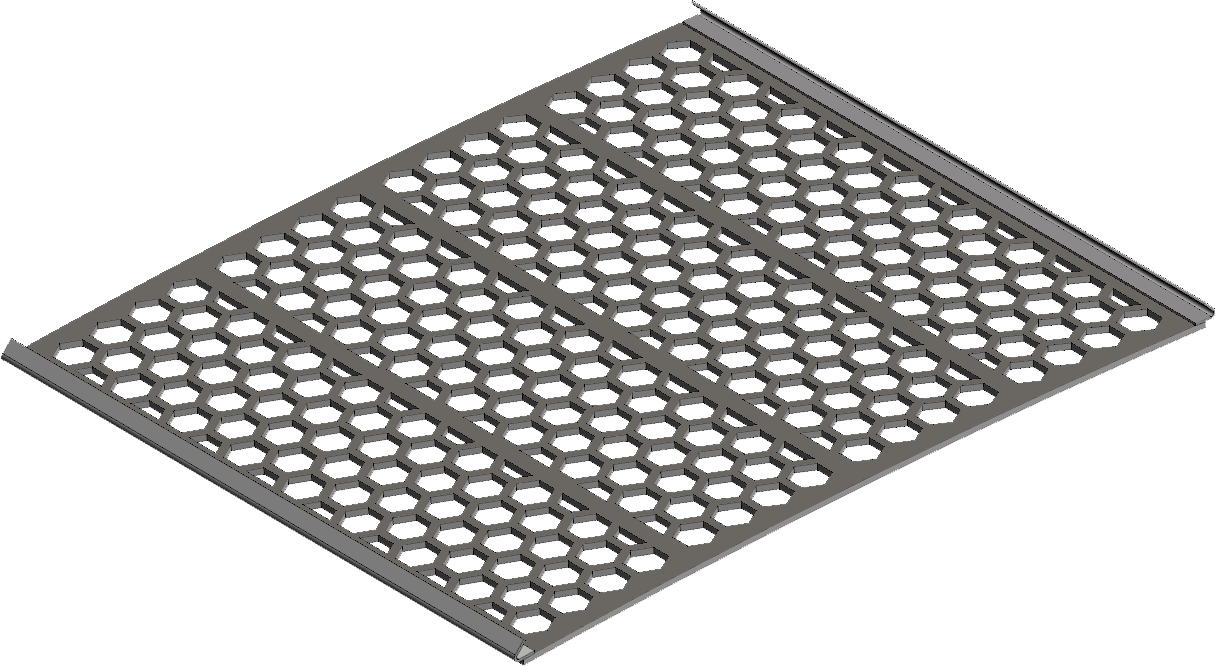
Side-Tension
Hooks
The hooks shown below are examples of common types, however, the hook shape, as well as the backleg and throat dimensions, can be customized for any machine.
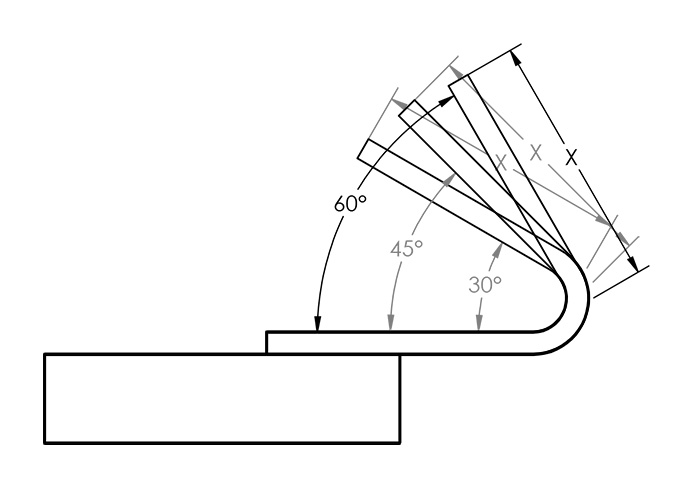
30 - 60 Hook
Common Side-Tension Hook Style
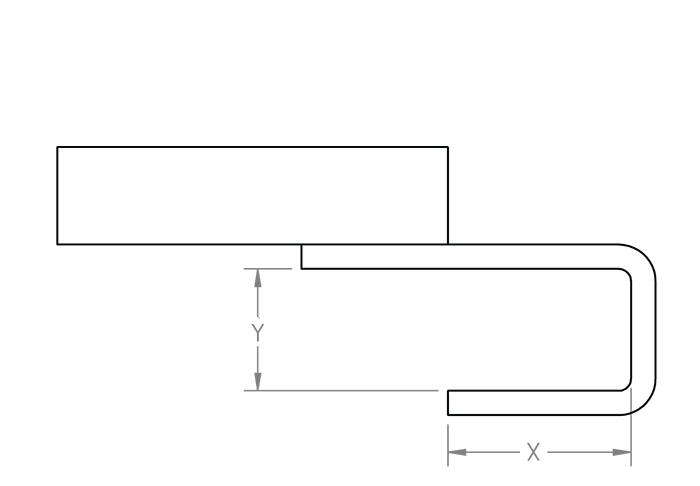
Square Hook
Common End-Tension Hook Style
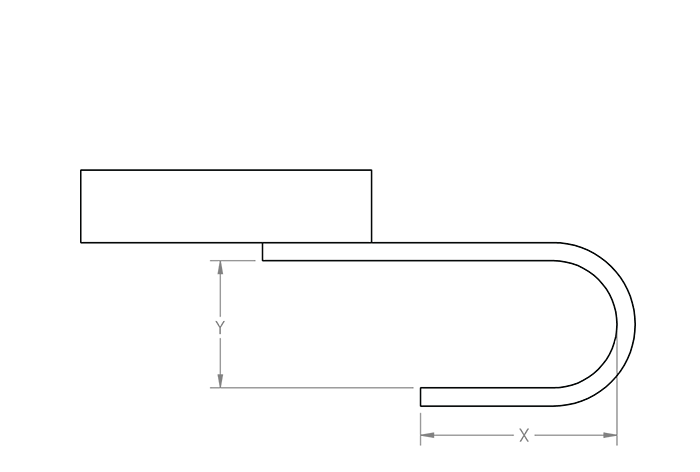
U Hook
Common End-Tension Hook Style
Opening Size | MAX 235 | MAX 400 |
---|---|---|
1″ – 2.5″ | 3/8″ Thick | 3/8″ Thick |
1.5″ – 4″ | 1/2″ Thick | 1/2″ Thick |
2″ – 8″ | 3/4″ Thick | 3/4″ Thick |
Speak to a Representative | 1″ Thick | |
Speak to a Representative | 1 1/4″ Thick |
Standard Hole Shapes
Square
Round
Hex
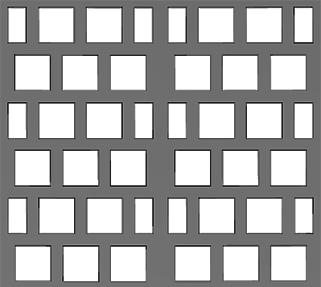
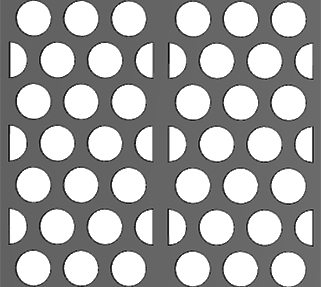
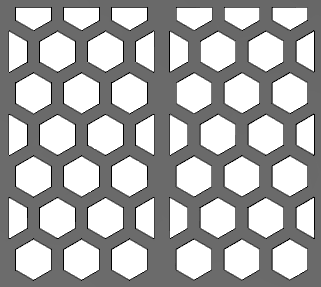
Custom Hole Shapes
If it can be drafted in AutoCAD, it can be burned on our HD plasma table! Speak to one of our knowledgeable Customer Service Reps to design a custom Perforated Plate solution for your unique job.
A few examples of unusual custom hole shapes and patterns that we have designed for other customers:
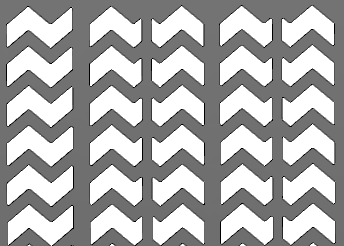
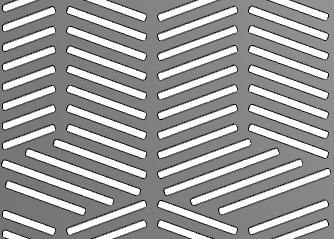
Blank Out Areas
Skid Bars
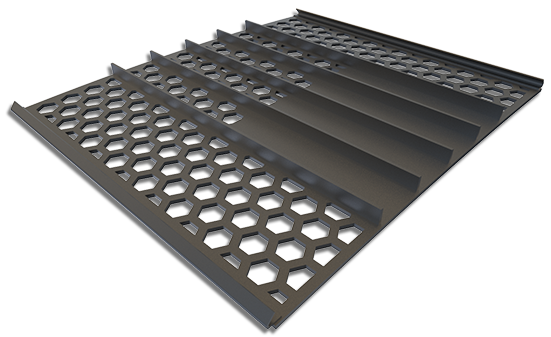
Custom blank out areas can be specified for any impact zone or high abrasion area
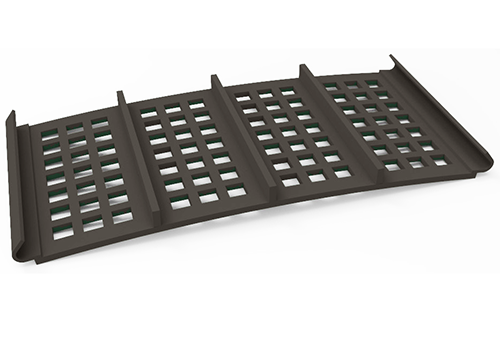
Skid Bars 2″ high X [your specified plate thickness] can be welded onto the screen surface, running parallel with material flow
Screen Configuration
Tips
Maximize wear life & screening productivity – by understanding the benefits and trade-offs of each Perforated Plate/Punch Plate screen configuration option.
Blank Outs
Strategically placed blank-out areas can offer significant wear life benefits by protecting the screen surface in high impact zones, without sacrificing thru-put.
Skid Bars
These 2” high steel bars, welded onto the screen’s surface, running directionally with material flow, can serve multiple functions. Skid bars shield the screen surface from high impact oversize material while allowing spec material to pass through – essentially screening material in two planes! Skid bars also help channel material, distributing it evenly along the screen’s surface, speeding up stratification and eliminating high wear points.
Plate
Thickness
A major benefit of the perforated plate design, is the fact that it can be configured for optimal Wear Life and Open Area! The overall thickness of a traditional wire screen is determined by the thickness of the wire itself. Thus, a thicker screen requires thicker wire, which necessarily takes up more space between each opening, reducing overall open area. A thick steel plate can be configured with closely arrayed holes for maximum Wear Life and Open Area!
*Note: A moderate trade-off between plate thickness and open area will exist in an inclined deck installation. The effective open area of each hole decreases as the deck incline increases. Horizontal decks will not see a reduction in open area as plate thickness increases.
Steel Type
MAX 235
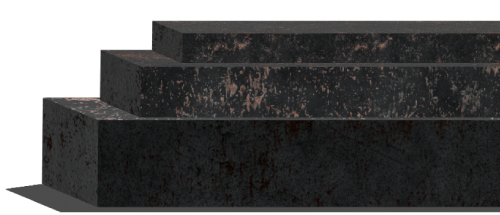
WHEN TO USE:
✓ Low to High Impact Material
✓ Low to Med Abrasive Material
WHEN NOT TO USE:
✗ Severely Heavy Impact Material
✗ High to Severely Abrasive Material
Vs.
MAX 400
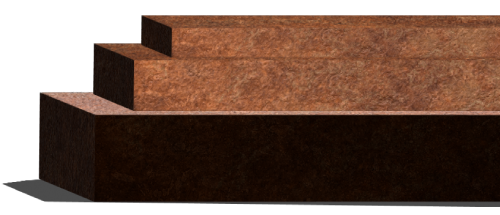
WHEN TO USE:
✓ Med to Severely Heavy Impact Material
✓ Low to Severely Abrasive Material
WHEN NOT TO USE:
✗ Not necessary for Low Abrasion Materials
✗ Not necessary for Low Impact Materials
Hole Shape & Pattern
High Open Area
Structural Strength
DID YOU KNOW? The efficiency of the Hex shape & pattern allows for the highest % of Total Open Area? Calculate your Hex production advantage using the calculator below!
DID YOU KNOW? Staggering your hole pattern improves structural strength and increases thru-put by ensuring that material can’t ride the length of the deck without being presented with an opening!
High Open Area
Structural Strength
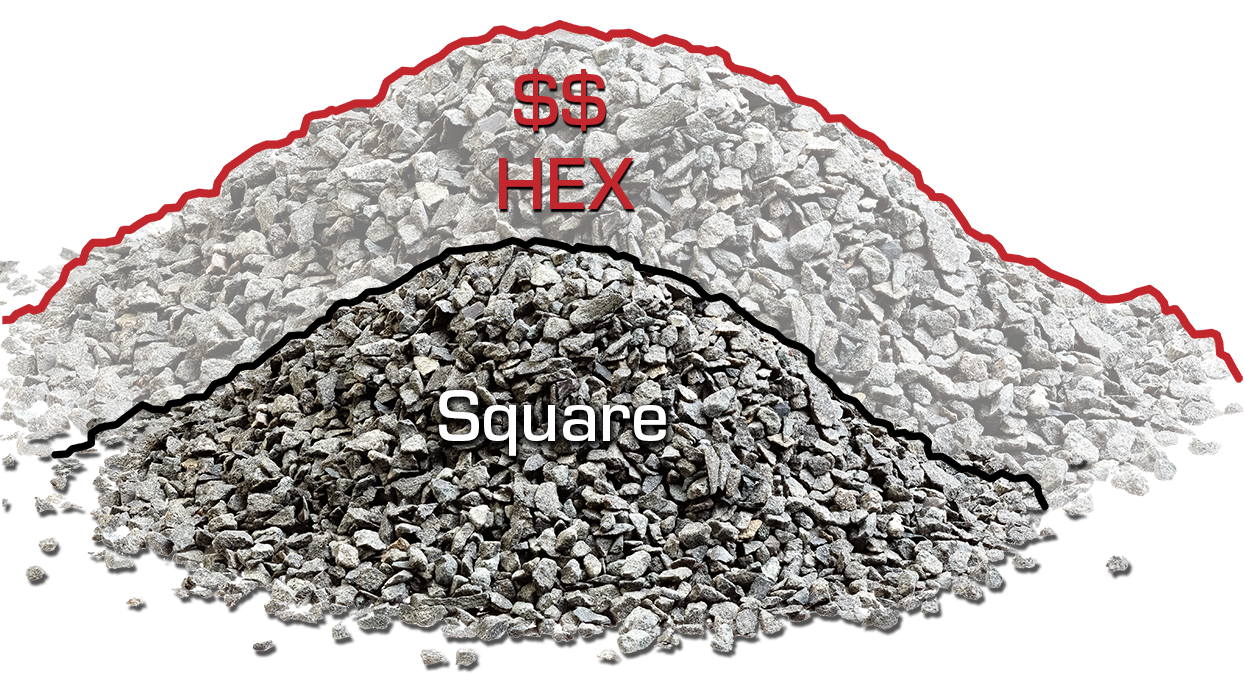
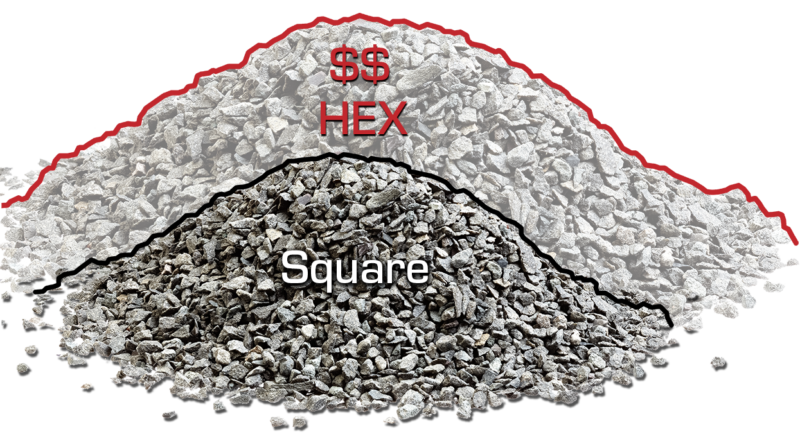
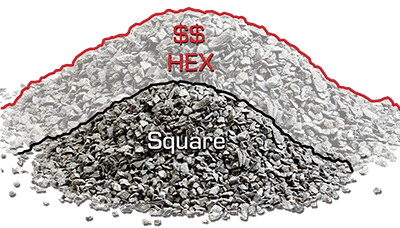
Did You Know?
A HEX opening provides more open area than a SQUARE, with the same sizing restrictions?
Did You Know?
A HEX opening provides more open area than a SQUARE, with the same sizing restrictions?
Did You Know?
A HEX opening provides more open area than a SQUARE, with the same sizing restrictions?
A Hex opening can be 1.12 times larger than a square opening, while maintaining the same average particle clearance. This means you get 8.72% more open area with the same sizing control!
Use the Calculator below to see how this simple switch could effect your production!
A Hex opening can be 1.12 times larger than a square opening, while maintaining the same average particle clearance. This means you get 8.72% more open area with the same sizing control!
Use the Calculator below to see how this simple switch could effect your production!
A Hex opening can be 1.12 times larger than a square opening, while maintaining the same average particle clearance. This means you get 8.72% more open area with the same sizing control!
Use the Calculator below to see how this simple switch could effect your production!
HEX Production Calculator
How it works
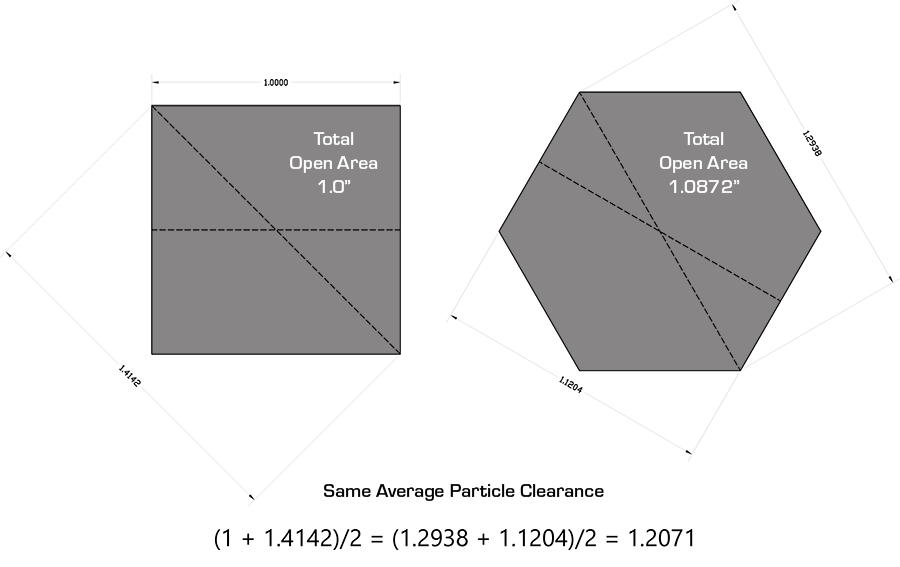